|
However, as the level of performance demanded of tires grows ever higher, 4D NANO DESIGN has reached its limits in terms of rubber analysis precision and the scale of simulations. And so, further technical advancement has now become necessary in order to achieve simultaneous improvements in such inherently contrary tire performance traits as fuel efficiency, wet grip and wear resistance.
|
Our new ADVANCED 4D NANO DESIGN enables us to analyze and simulate the internal structures of rubber accurately and continuously from the nano-scale to the micro-scale in order to achieve simultaneous improvements in the inherently contrary 3 Key Tire Performance Traits: fuel efficiency, wet grip and wear resistance (Figures 1, 2). Using the SPring-8*1 Large-Scale Synchrotron Radiation Facility to analyze the structure of rubber and the world-class J-PARC*2 Proton Accelerator and Experimental Facility to analyze the behavior of rubber through experiments involving neutrons and other elementary particles, we are now able to clearly observe the internal structures and molecular behavior of rubber. As a result, we have succeeded for the first time in capturing the heretofore unseen structures and behavior of polymer at the silica interface, the heterogeneity of sulfur crosslinking, the distribution of sulfur crosslinking lengths, the behavior of silica networks and so on. Further, utilizing the processing power of the K*3 computer to analyze the data so obtained, we are now able to run large-scale simulations at the molecular scale, making it possible to identify the locations of stress and heat generation within rubber (Figure 3). After minutely analyzing the behavior of atoms and molecules in these simulations, we have learned that the causes of stress and heat generation within rubber are closely linked to silica network behavior, crosslinking structures and silica interface polymer behavior (Figure 4). Using this discovery as a launching point, we have developed "Stress Control Technology," a new technology that enables us to simultaneously improve the 3 Key Tire Performance Traits, which are inherently contrary (Figure 5). For example, focusing our attention on wear resistance, we found that when conventional rubber is deformed, scattered points of stress can cause gaps to form among the rubber molecules. These gaps, called voids (Figure 6), are one of the causes of wear. In response to this finding, we applied our Stress Control Technology to produce rubber with a high degree of control over the types of stress that cause these voids to form, thus making it possible to suppress the formation of voids while at the same time also controlling the generation of waste heat (Figure 6, Right). Thus, we have succeeded in developing rubber that achieves an enormous improvement in wear resistance while maintaining high fuel-efficiency and wet grip performance. Now, we have produced our Tire with Wear-Resistant Max Tread Rubber as a concept tire to demonstrate the capabilities of Stress Control Technology. While maintaining conventional fuel efficiency and wet grip performance, the tread rubber used in this concept tire achieves a 100%*6 increase in wear resistance. In the future, further utilization of Stress Control Technology will make it possible to freely control and simultaneously improve all of the 3 Key Tire Performance Traits. Using our new ADVANCED 4D NANO DESIGN, Sumitomo Rubber Industries will further increase the pace of our development of new materials as we continue to provide our customers with environmentally friendly high-performance tires at reasonable prices.
|
| *1 | SPring-8 is the world's most powerful synchrotron radiation facility. (Location: Sayo, Hyogo, Japan) |
*2 | J-PARC is a proton accelerator and experimental facility that is used for cutting-edge research. (Location: Tokai, Ibaraki, Japan) |
*3 | K is one of the world's most powerful supercomputers in terms of processing capabilities. (Location: Kobe, Hyogo, Japan) |
*4 | This is a concept tire and, as such, there are no current plans to make it available for sale. (Max: Refers to our company's highest grade of tread rubber. Tread: The part of a tire that is in contact with the road.) |
*5 | Compared to our company's previous models. |
*6 | Compared to the tread rubber used in our company's tires in 2011. |
|
| |
| <Collaborating Organizations> |
| | Large-Scale Synchrotron Radiation Facility SPring-8 |
| Proton Accelerator & Experimental Facility J-PARC |
| RIKEN Advanced Institute for Computational Science (K computer) |
| High Energy Accelerator Research Organization Institute of Materials Structure Science |
| Frontier Soft-Material Beamline (FSBL) Consortium |
| University of Hyogo Institute for Research Promotion and Collaboration, Synchrotron Radiation Research Center |
| JSOL Corporation |
|
| <Joint R&D Collaborators> |
| | Professor Yoshiyuki Amemiya and Assistant Professor Yuya Shinohara, Tokyo University Graduate School of Frontier Sciences |
| Professor Yuichi Masubuchi, Nagoya University National Composite Center |
| Associate Professor Tadanori Koga, Stony Brook University |
|
| <Participating/Collaborating Projects> |
| | Photon and Quantum Basic Research Coordinated Development Program |
|
| |
| [Figure 1] |
| Analytical Range of 4D NANO DESIGN and ADVANCED 4D NANO DESIGN |
| 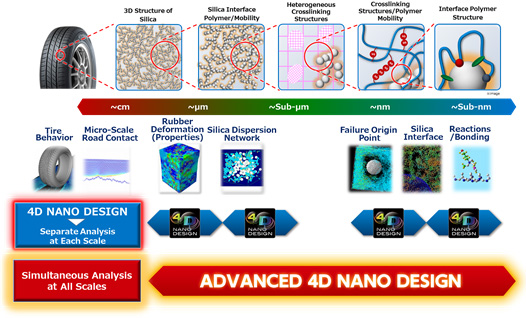 |
| |
| [Figure 2] |
| Simultaneous Improvement of the 3 Key Tire Performance Traits with ADVANCED 4D NANO DESIGN |
| 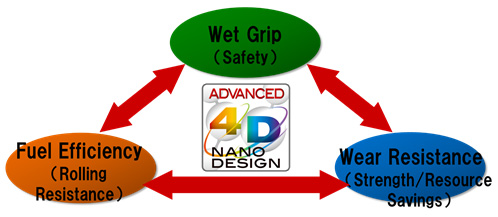 |
| |
| [Figure 3] |
| Overview of Collaboration with Japan's Leading Research Facilities |
| 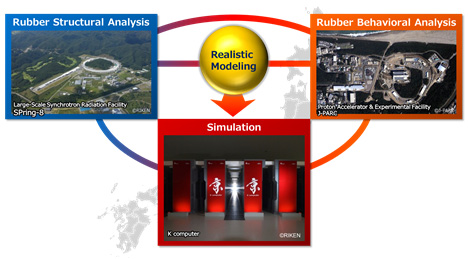 |
| |
| [Figure 4] |
| Identification of Locations of Stress within Rubber |
| 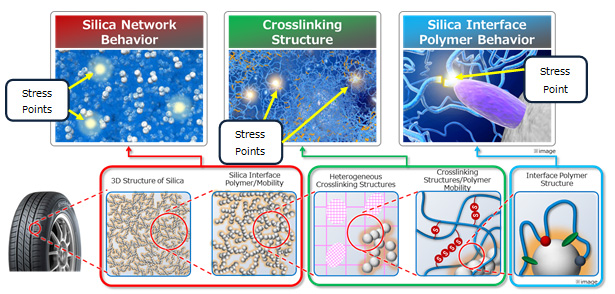 |
| |
| [Figure 5] |
| Establishment of Stress Control Technology |
| 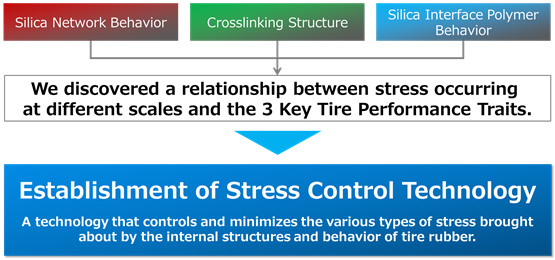 |
| |
| [Figure 6] |
| Suppression of Void Formation through Stress Control Technology |
| <Void Formation Conditions: SPring-8 High-Resolution X-Ray CT Scan Observation> |
| 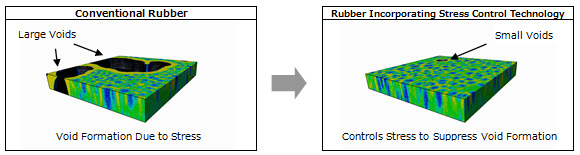 |
|
|